After four years of hard work, we are proud to showcase to the public the PHOTORAMA PV recycling pilot line! The pilot line demonstrates in real life conditions the solutions developed by the PHOTORAMA consortium to recycle and recover at high quality level components present in PV panels.
These processes were first revealed to the public on the 9th of April in the historic city of Tangermünde, Germany. Nearly 100 recycling and energy experts joined the event, eager to learn more about the high-end technologies developed by PHOTORAMA.
The day started with a detailed presentation of the recycling processes and their potential application. To close the technical inputs from the consortium, artist Judith Fegerl provided the audience with an alternative perspective on End of Life PV panels through her work recovering panels for artistic installations.
Morning session: Presenting the recycling processes
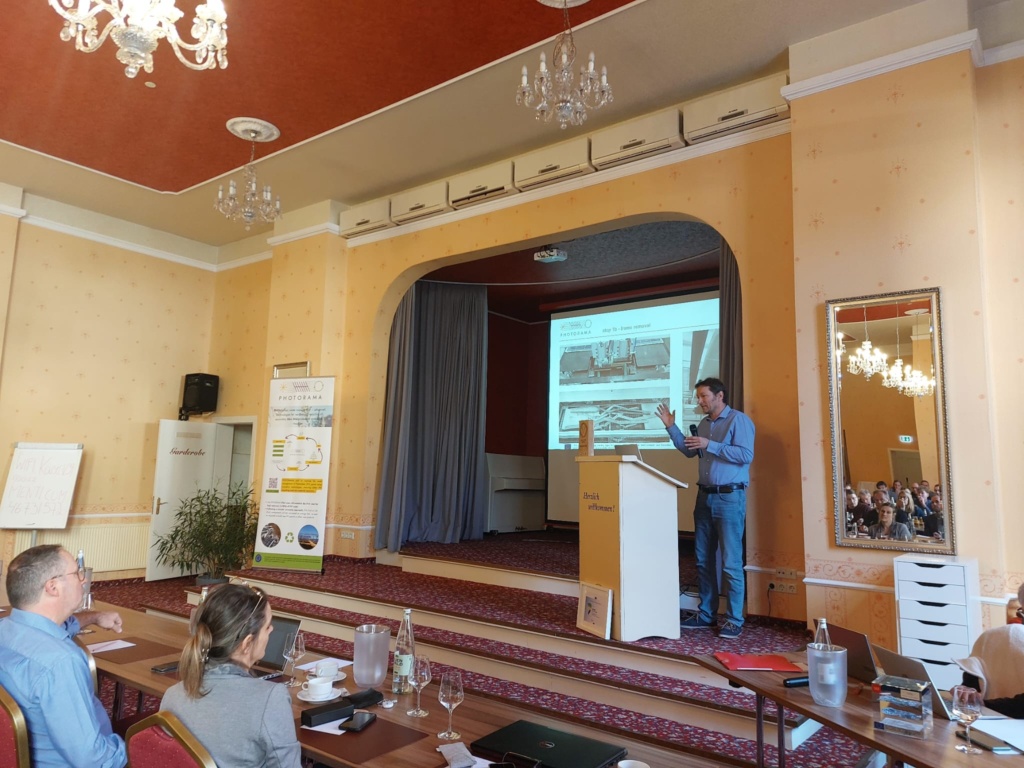
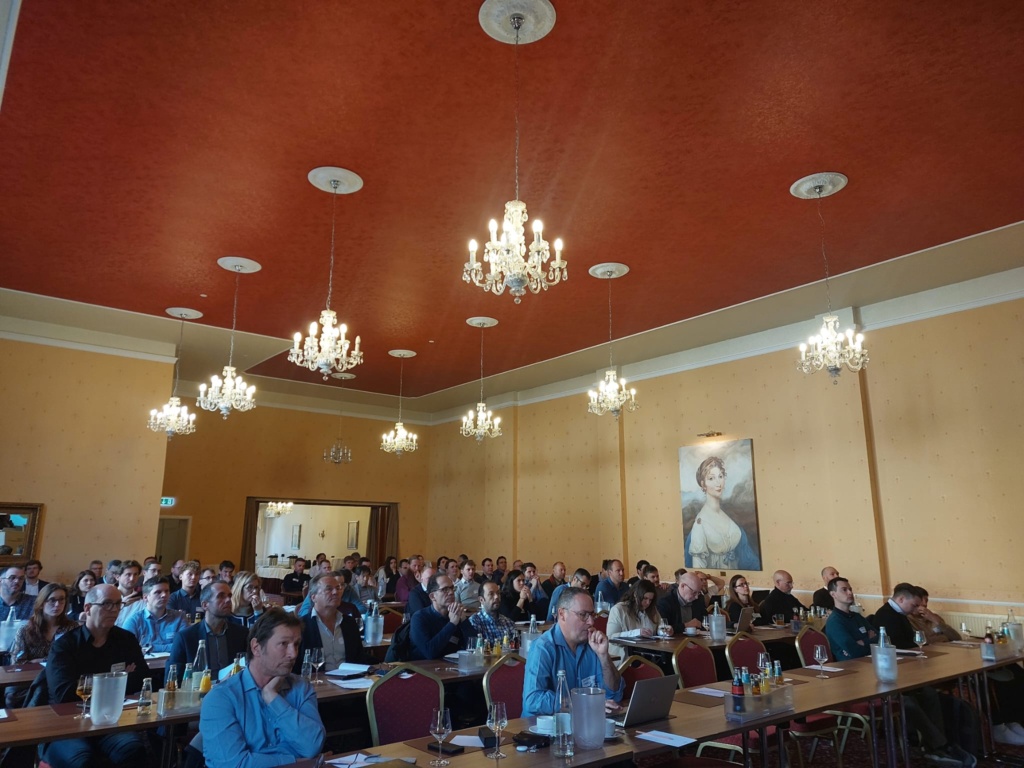
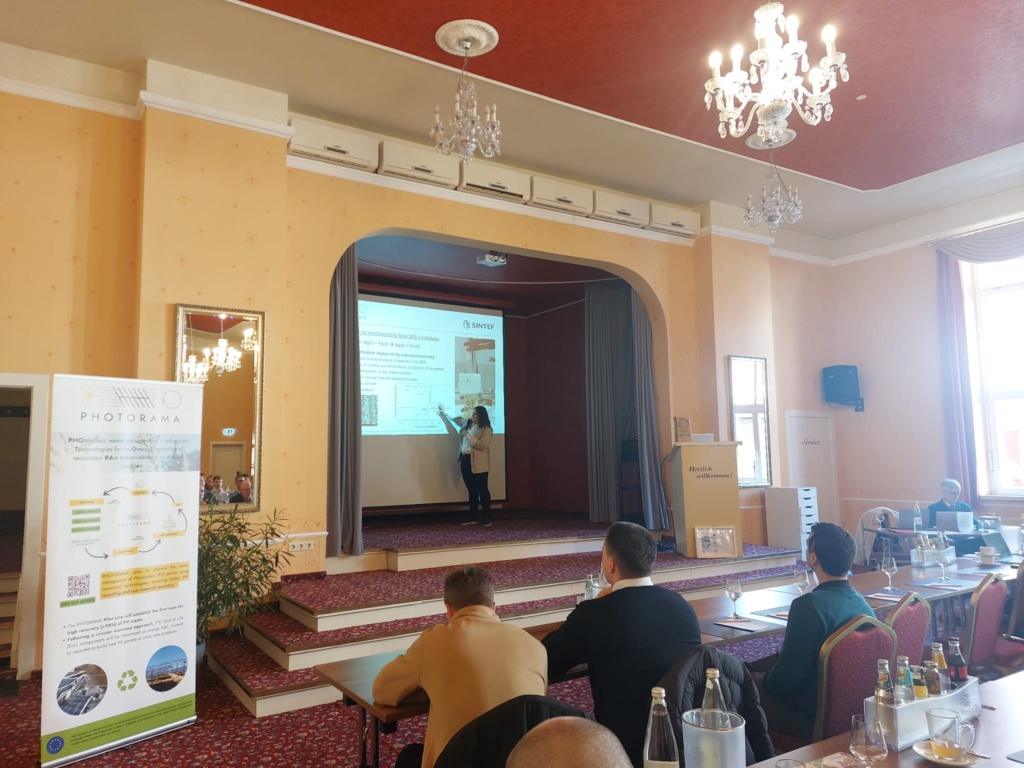
In the afternoon, participants took part in the visit of the pilot line at LuxChemtech facilities, where each process was showcased.
Afternoon session: pilot line visit at LuxChemtech facilities
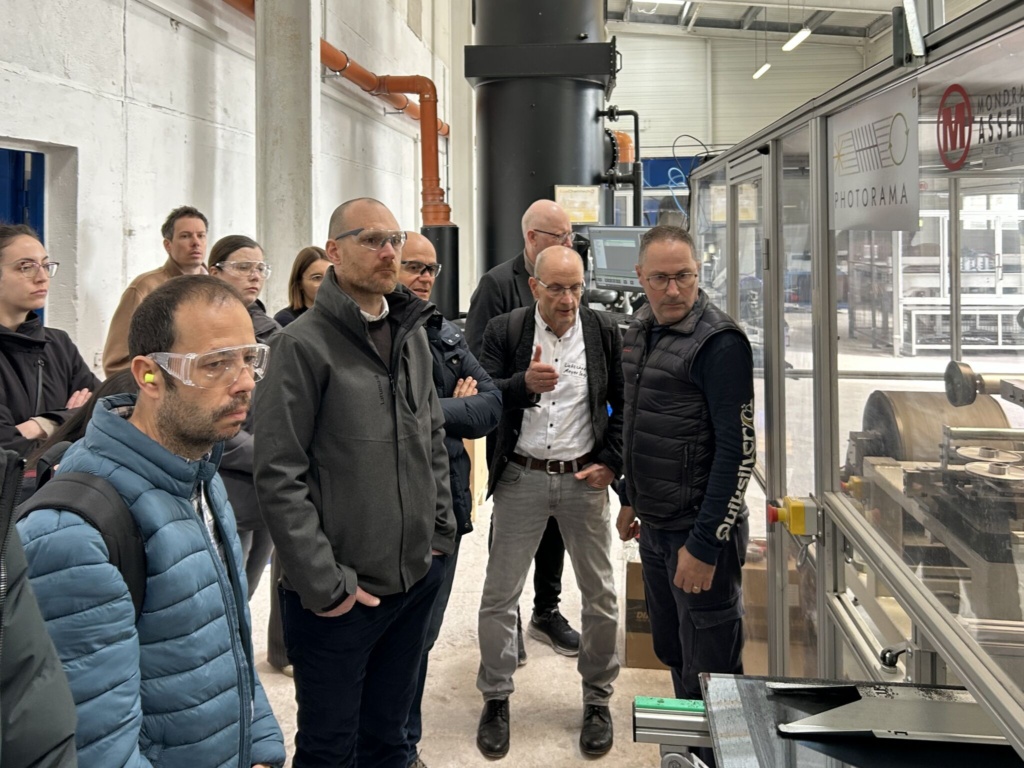
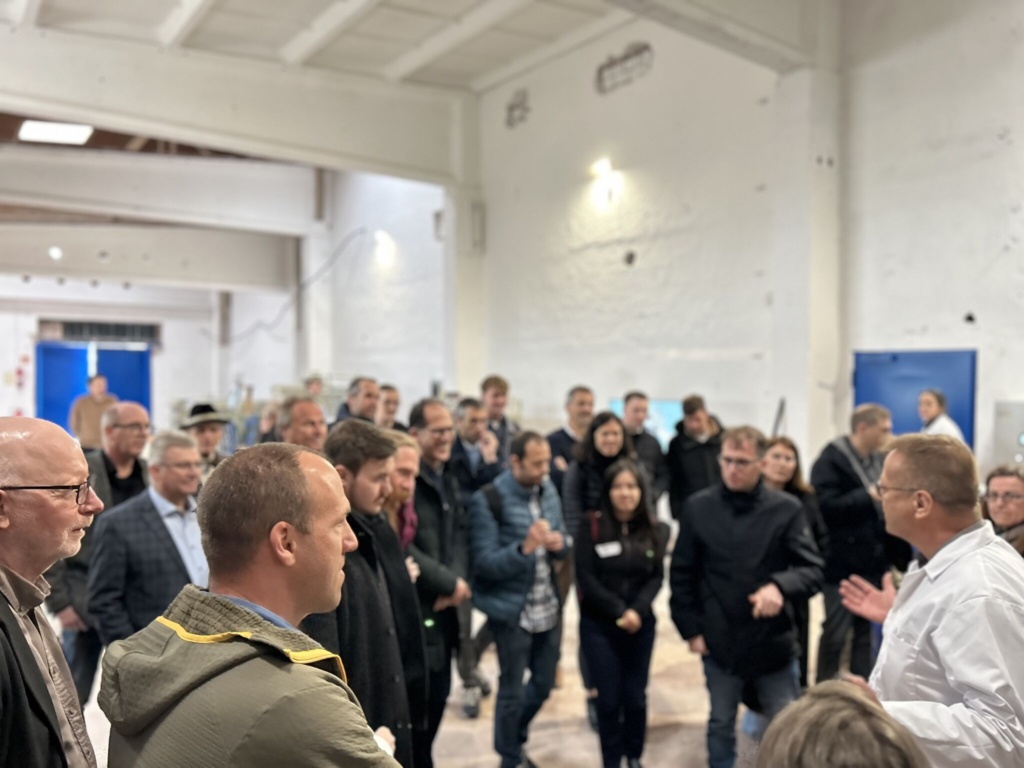
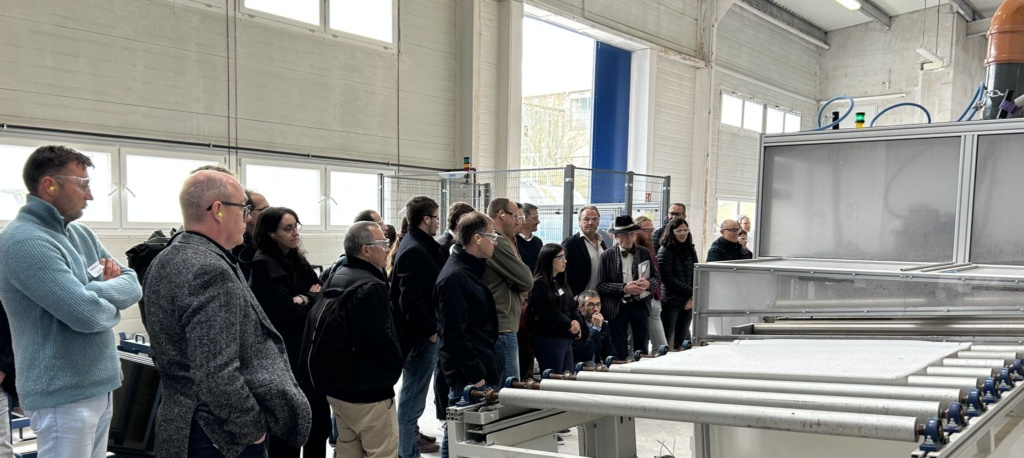
The three steps process used by the PHOTORAMA pilot line applies a combination of mechanical and chemical recycling technologies to recover PV materials at high purity levels
Step1: Frame & Junction box disassembly
The first step consists in removing the frame of the PV panels and its junction box that is split in two stations.
Step 2: Mechanical delamination
PHOTORAMA presented three different innovative processes used for the delamination of the PV panels, able to separate the different layers of the ‘PV sandwich’.
Diamond wire cutting
Diamond wire cutting is a process where a diamond wire is used to cut through the layers of the panels or for removing back rails of specific thin film modules. The PHOTORAMA technology is innovative for its high precision, relative speed and temperature monitoring capacities.
Flashlight
Thin film double glass PV panels can be delaminated with an optical technology by using a flashlight. The flashlight weakens the semiconductor layer/encapsulant contact with the glass sheets, and the panel can then be opened mechanically.
Water Jet
In this technology, high pressure water jets are used to proceed to the mechanical removal of polymers and solar cells. The technology developed by PHOTORAMA allows for high precision and is able to recover ultra clean glass.
Step 3: Metal recovery
Once the panel’s components have been separated the next step is to recover metals from these components. This is done by using two main techniques:
Leaching and Electrowinning
Deep Eutectic Solvent leaching and Electrowinning processes are used to recover silicon and silver to purity.
Methane Sulfonic Acid & Electrowinning
Another process uses Methane Sulfonic Acid in combination with electrowinning to recover the Indium and Gallium in CIGS panels and the Silver, Indium and Silicon from c-Si HJT cells. This process allows for a recovery of metals at high purity level.
The recovery of silver was demonstrated at the pilot line visit.
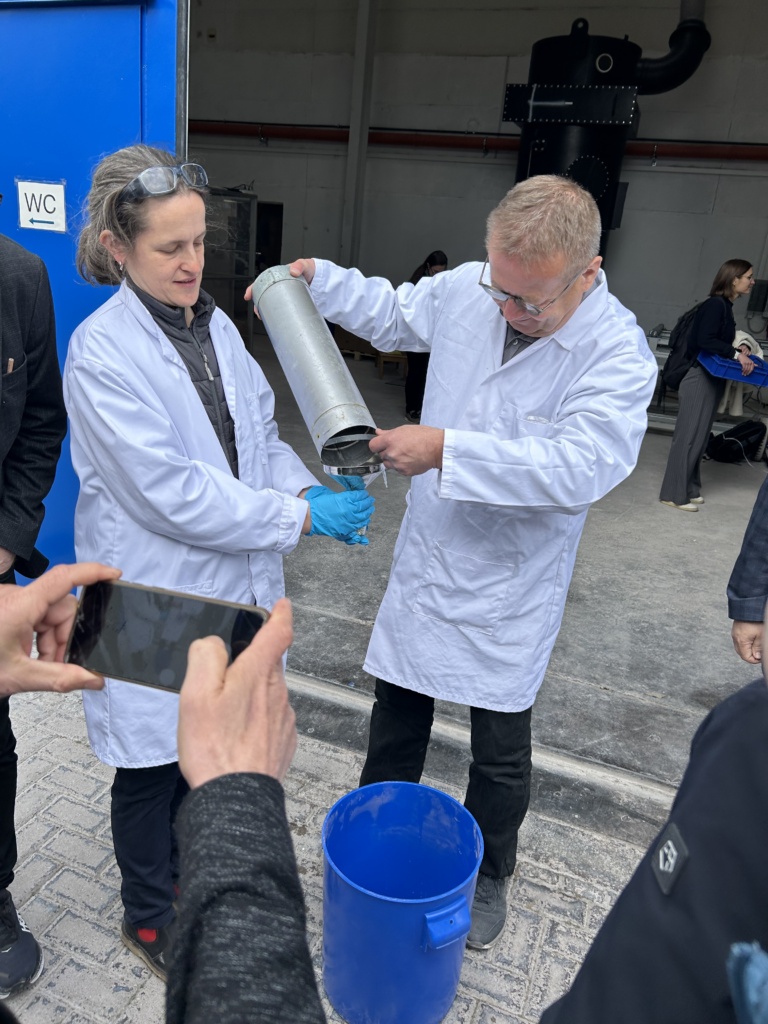
Complementary programme
In addition to the technical demonstration, participants were also offered the possibility to take part in a guided tour of the historic city of Tangermünde, before enjoying a networking dinner at the town castle.
The next day, the PHOTORAMA consortium met for its last consortium meeting before the end of the project. It was the occasion to reflect on the pilot line visit, the work done so far and the next steps in the PHOTORAMA success story!
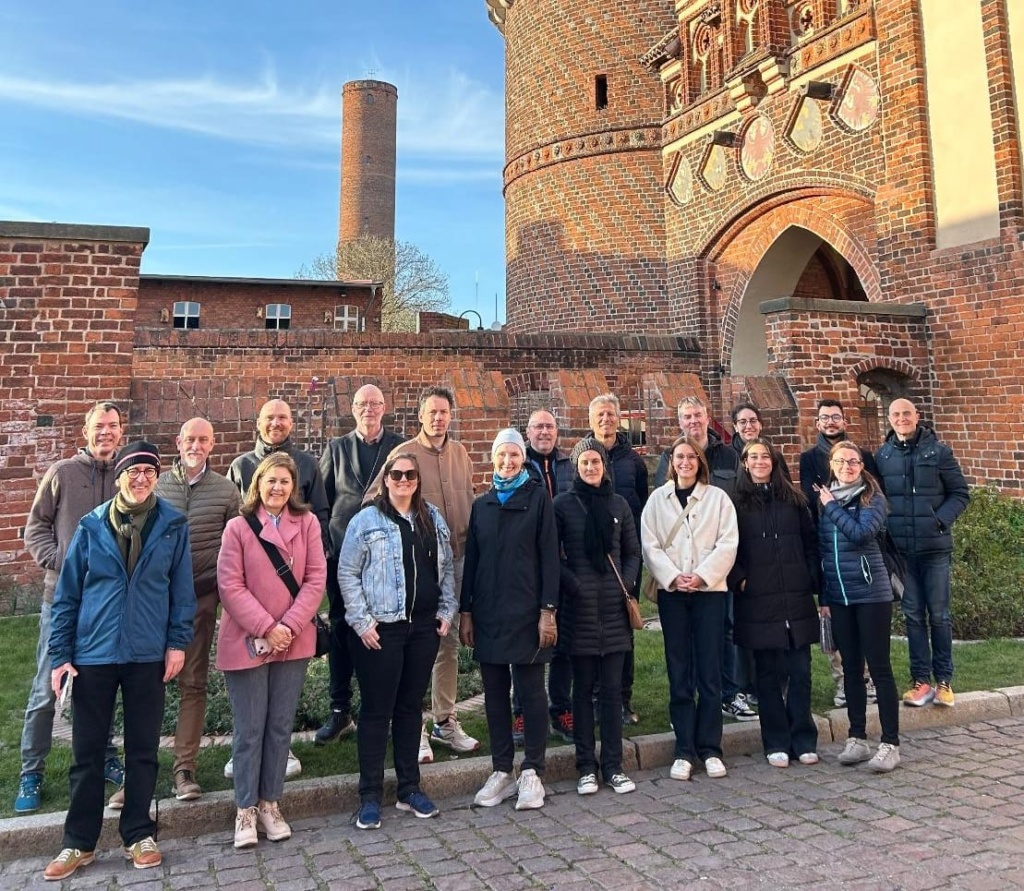